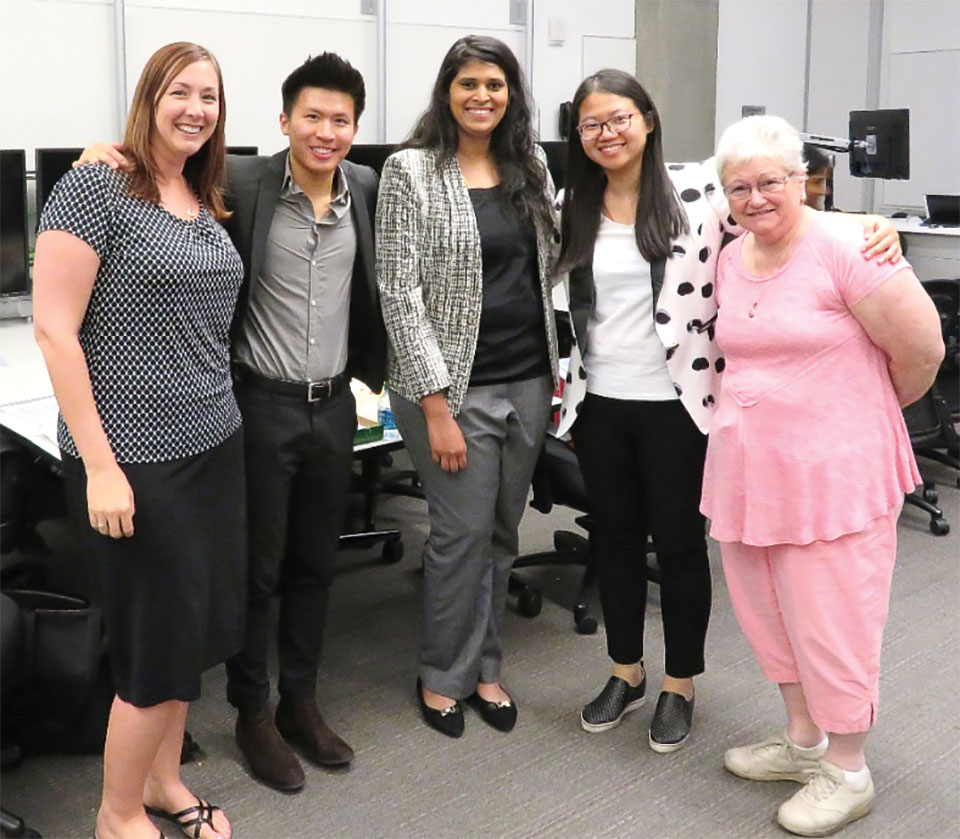
Left to right: Leanne Leonard, Trey Tan, Monisa Manju Nagarajan Gomathi, Xiao Xiao Lyu and Edna DeFord
Dr. Stephen Kirk
PebbleCreek Community Church (PCCC) has long been involved with Agua Fria Food and Clothing Bank. This spring members of the PCCC Mission Committee worked with Dr. Stephen Kirk (professor at Arizona State University School of Sustainable Engineering and PebbleCreek resident) and Leanne Leonard (Executive Director of the Food Bank) to improve Agua Fria’s processes around food, clothing and toy distribution, particularly over the Thanksgiving and Christmas holidays.
Edna DeFord, chairman of the Mission Committee, noted that prior to the holidays Agua Fria is packed with people waiting for food, clothing and toys. PCCC assists in the distribution and DeFord wanted to help improve the process. Dr. Kirk saw this as an opportunity for graduate students from his class on value engineering (VE) to gain practical experience by assisting Agua Fria in a semester project. The goal of this project was to improve the efficiency and productivity of the distribution process through innovation and eliminate any form of waste, such as time, manpower or resources. Preserving the dignity of the customers receiving the distribution was also important.
Agua Fria Food Bank serves some 500 families over Thanksgiving and Christmas annually. Hence, this VE study started with an evaluation of existing conditions and ended with design recommendations to improve the building layout and distribution process, particularly on events such as Christmas and Thanksgiving.
A student team was formed as part of Dr. Kirk’s course on value engineering. Students included Monisa Manju Nagarajan Gomathi from India, Xiao Xiao Lyu from China and Trey Tan from Singapore. They visited the food bank to meet with Leonard. She explained the current processes and gave them a tour of the facility. The students returned several times to prepare drawings of the facility and ask follow-up questions. They then analyzed the process and prepared a function analysis of the requirements. Next the students brainstormed a number of ideas for improvements. Based on specific functions and criteria, the ideas were evaluated and the better ones developed into proposals for process improvements.
The VE Team’s specific objectives included:
* Shorten the waiting time for food collection
* Improve the process through value engineering methodologies
* Improve customer satisfaction ratings
* Simplify the current environment in order to provide easier and more effective food recognition and navigation
The results:
* 96 ideas were identified for improving the distribution process.
* 20 ideas were highlighted for further consideration.
* Building layout process flow modifications were made to improve distribution time to customers.
Leonard summed up the student final presentation by saying, “I was impressed with their presentation and the work that they put into understanding the current process. They seemed truly passionate about wanting to find ideas and solutions that would make a significant difference in the work we do. As always I am so thankful for the continued partnership with the PCCC and its amazing congregation members!”